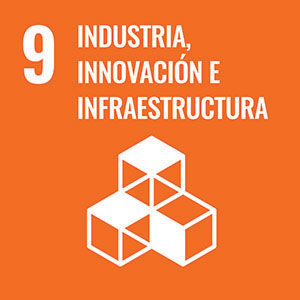
ASTURIAS
ArcelorMittal: la innovación en el acero tiene acento español
La multinacional cuenta en Avilés con tres centros donde pone a prueba algunos de sus proyectos más avanzados en el área de I+D
Pablo Garcinuño
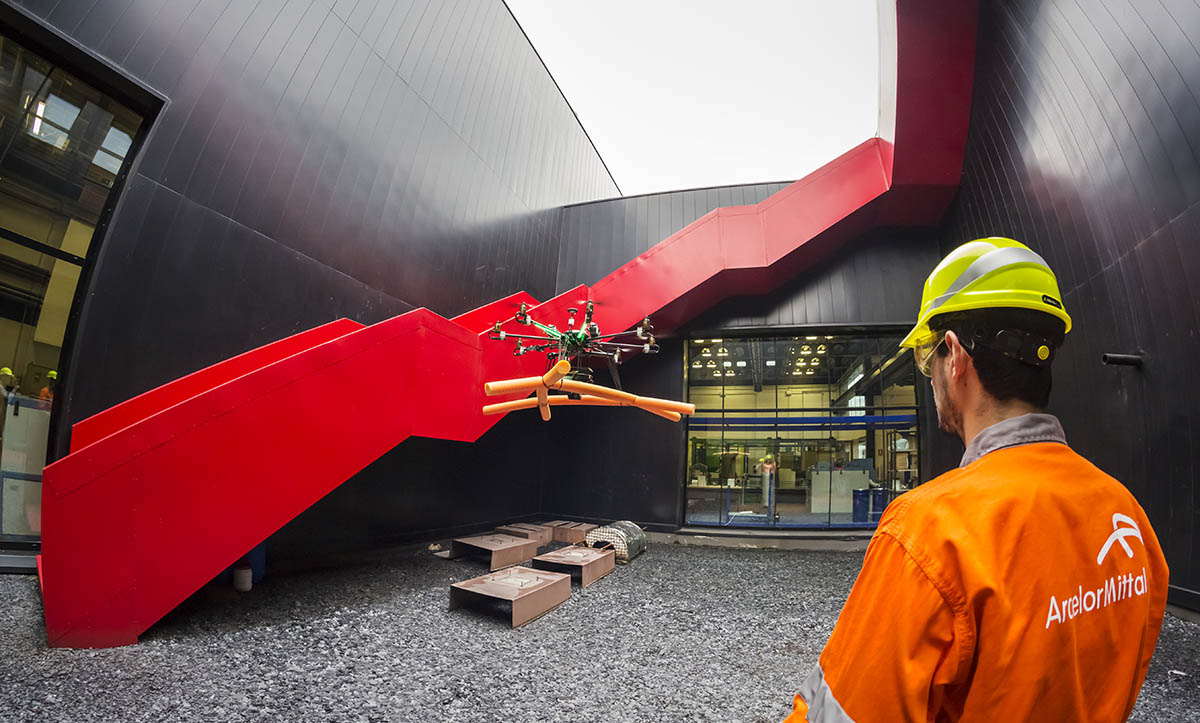
Está en los edificios. También en los coches tiene una gran presencia y sus características varían según la pieza y su ubicación dentro del vehículo. Miremos donde miremos, lo encontramos. Incluso está en las latas de conserva. “La sociedad actual sería impensable sin el acero”, señala Pedro Prendes, Global R&D Process Portfolio Leader en ArcelorMittal, la compañía que, en alguna de sus campañas publicitarias, bautizó a este material como ‘La fibra de la vida’. ¿Cuál es su secreto? “No hay ningún otro material que pueda llegar a tantísima gente”.
En nuestro día a día no somos conscientes de esta omnipresencia del acero. Tampoco de la innovación que hay detrás de él. La siderurgia se ha aliado desde hace décadas con la tecnología y su evolución en este campo ha sido exponencial. El material de hoy no es el mismo que se fabricaba tiempo atrás –más del 70 por ciento de los aceros que lleva actualmente un coche no existían hace 20 años–. Y aún continúan afrontando nuevos retos, como reducir su huella de CO2 a través de la descarbonización.
En todo ello resulta clave la investigación que realiza la propia compañía a través de sus centros de I+D. En España hay dos núcleos centrados en estas labores, uno en Sestao (Vizcaya) –la propia planta es un banco de pruebas para tecnologías rupturistas– y otro en Avilés (Asturias), que se ha convertido en los últimos años en toda una referencia de innovación a nivel internacional.
Todo cambió en una década
Aquí, en torno a la ría de Avilés, ArcelorMittal cuenta con dos centros –distribuidos en 17.000 metros cuadrados– volcados en investigar para mejorar el proceso siderúrgico y hacerlo más barato, más eficiente y más sostenible. ¿Pero por qué se ha convertido Asturias en un punto clave dentro del departamento de I+D de la compañía? Para entender los motivos hay que remontarse a 2008, cuando el actual Grid, por entonces CDT (siglas de Centro de Desarrollo Tecnológico), funcionaba con 24 personas casi exclusivamente centrados en las necesidades de las plantas locales del Principado.
En ese año asume la dirección Nicolás de Abajo y todo cambia. Prueba de ello es que, diez años después, este asturiano pasó a dirigir todos los centros de I+D de la compañía a nivel mundial. Y otros dos españoles, Carlos Alba y Pedro Prendes, forman parte del comité de dirección de dicho área. Nuestro país está más presente que nunca en la maquinaria de innovación de ArcelorMittal
Aplicar modelos de inteligencia artificial a las factorías para predecir cuándo una máquina va a fallar es uno de los muchos avances que ha logrado ArcelorMittal
Y las razones hay que buscarlas aquí, en Avilés, en esa época que, además, era el inicio de la crisis económica. Ni eso impidió que el centro haya ido creciendo hasta contar en la actualidad con más de 300 investigadores. El secreto, según el propio Nicolás de Abajo, radica en “la motivación de un equipo que creyó que se podía hacer innovación del más alto nivel en Avilés”.
Desde julio de 2018, lidera a los 1.500 investigadores que se reparten en los 16 laboratorios que la compañía tiene por todo el mundo –con un presupuesto cercano a los 300 millones–. Su primer año en el cargo, asegura, se ha centrado en “escuchar mucho” y en “decidir conjuntamente cómo queremos transformarnos”. Ambas líneas han servido para elaborar un plan de I+D que sirva de mapa a seguir.
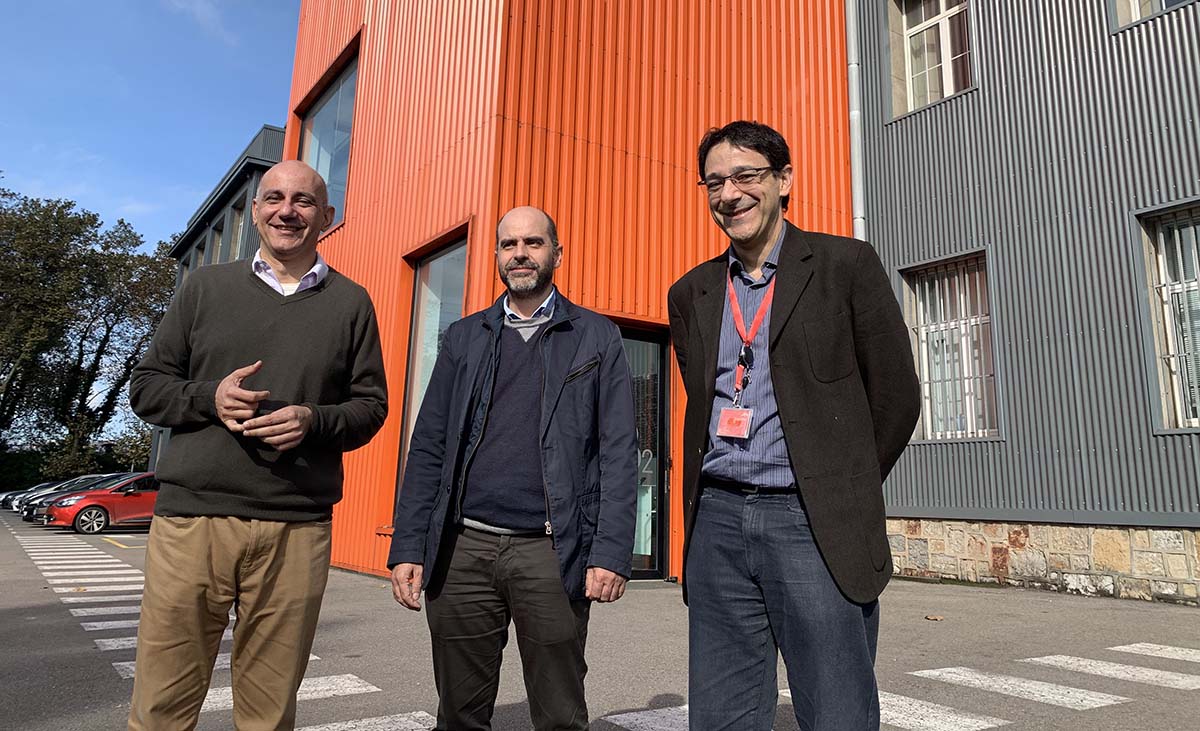
Nuevas Fronteras
En 2014 abrió sus puertas en Avilés el centro New Frontier (Nuevas Fronteras) “con la idea de explorar cómo esas megatendencias que en aquel momento se decía que iban a cambiar el mundo podían afectar a nuestra industria”, afirma el director de este área, Roberto Suárez.
Aplicar modelos de inteligencia artificial a las factorías para predecir cuándo una máquina va a fallar es solo un ejemplo de las muchos avances que están consiguiendo en campos como el big data, el machine learning o el internet de las cosas (IoT).
También trabajan en la investigación de nuevos materiales, tales como el grafeno, “el material milagroso del que todo el mundo habla”, dice Suárez. De hecho, en el campus New Frontiers cuentan con una planta piloto de fabricación de este producto a partir de los propios residuos de la acería, que genera grafito con bastantes impurezas.
Su objetivo es ser capaces de fabricar el grafeno de una manera escalable para pasar del laboratorio a una producción industrial a un coste aceptable, y controlar así la calidad del producto final. Lo que quieren es utilizar este material para mejorar el acero que fabrican y barajan distintas opciones, como un recubrimiento que lo proteja de la corrosión.
Lo más llamativo son los proyectos que utilizan el internet de las cosas (IoT, por sus siglas en inglés) para hacer que el acero sea comunicativo. A través del grafeno consiguen que unas planchas cambien de color y también que puedan comunicar ellas mismas la existencia de deformaciones o grietas en su interior.
Impresión 3D del acero
Además de los campus Grid y Nuevas Fronteras, ArcelorMittal decidió ubicar en Avilés su centro de impresión 3D de metal, una instalación de referencia a nivel nacional e internacional que ya se está utilizando para fabricar piezas de repuesto destinadas a las propias fábricas de la compañía. Para estas labores incluso se ha creado una spinoff denominada Thesteelprinters.
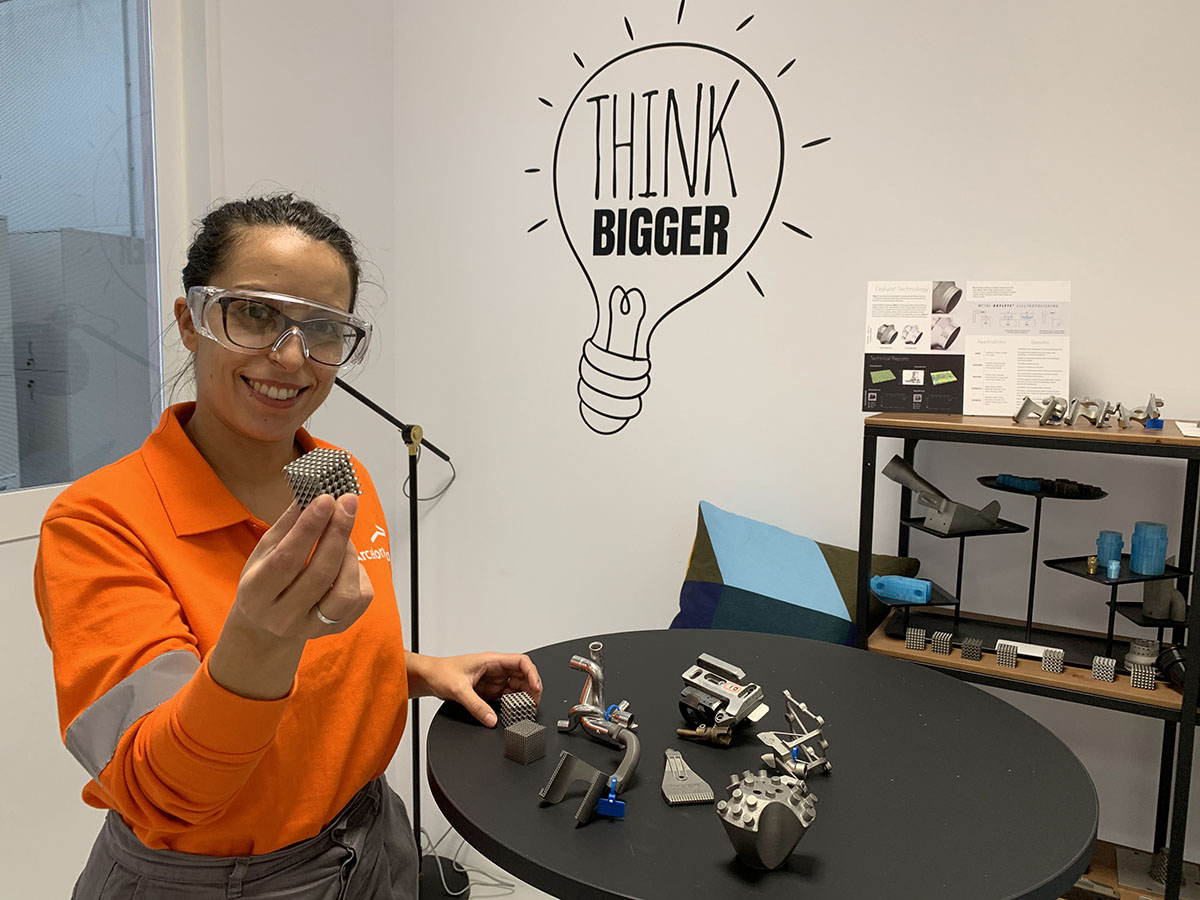
Las ventajas de la fabricación aditiva de la impresión 3D (frente a la tradicional, que es sustractiva, es decir, hay que hacer los huecos de los espacios que quedan en vacío) es que permite geometrías complejas anteriormente imposibles de hacer. Con los métodos tradicionales nunca hubieran podido conseguir conductos milimétricos curvos en el interior del acero, por poner solo un ejemplo.
En este centro cuentan con su propio atomizador, que es donde consiguen el polvo de acero (aunque también investigan con otros materiales) que luego utilizan en la impresión 3D. Esas partículas son las que se van soldando capa a capa a través de tecnología láser, por lo que se puede dar la forma que se desee a cada pieza. Prácticamente no hay limitaciones.
Gestión de residuos
Volvemos al Campus Grid para visitar el área que se dedica a mejorar la gestión de residuos. Los lodos que se obtienen en la extracción minera del acero se suelen depositar en balsas estériles que hay que vigilar muy de cerca para evitar desastres como el ocurrido en Aznalcóllar a finales de los noventa, o en Brasil el año pasado.
Se trabaja día a día en hacer estas presas más seguras. Uno de los factores a tener en cuenta es que, cuanto más agua tienen esos residuos, más inestables son. Por eso se ha avanzado mucho en toda la tecnología relacionada con el espesamiento del lodo. Además, las balsas están monitorizadas con una red de sensores y se vigila su evolución a través de satélites, drones e incluso robots anfibios que permiten entrar en el interior para realizar estudios in situ.
Además, se dedican a reducir los residuos producidos. Y, lo que es más importante, a darles una segunda vida reutilizándolos. Hay que tener en cuenta que para producir un kilo de acero se generan 1,4 kilos de escoria, que puede ser utilizada, por ejemplo, para la construcción de carreteras.